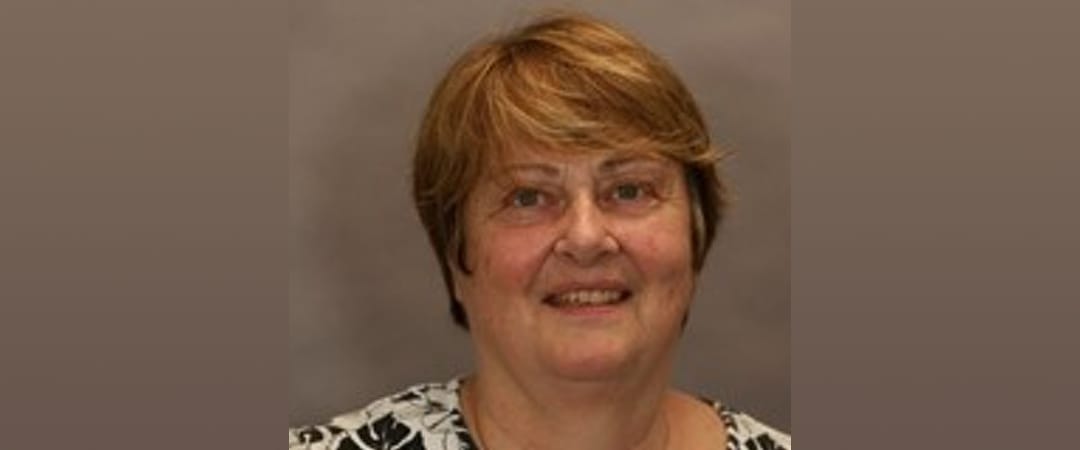
Meet the Expert: Virginia A. Lang, PHD
President and Chief Scientist, HirLan International SA
Virginia entered the medical research field as a Coordinator of Research at the Clinical Research Unit Kennedy Institute of Johns Hopkins Medical Center. From there, she moved into the field of Human Factors through the doctoral program at SUNY Binghamton. In July 2014, Virginia founded and established the HirLan Institute of Human Factors with labs in Carlsbad, Calif. and a Consortium arrangement in London. Because the FDA requires medical device companies to include performance testing results in their submissions, human factors engineering is an effective process that measures cognitive, behavioral and physical involvement with pharma and medical devices. We discussed with her the importance of using human factors engineering at the onset of new product development to produce products more efficiently and quickly with greater potential for approval.
What is human factors engineering? How would you define it?
Human factors engineering studies how people are going to interact with something—something as simple as a ball point pen or very complicated such as a DaVinci system for conducting surgery. It looks at three different components–cognitive, behavioral and physiological. Cognitive processing is what the human does when they are interacting. Behavioral looks at what they are doing, and physiological examines whether the product meets the physical constraints of the user’s physiology such as standing requirements. These three components substantially influence how the device is used whether we’re talking about using a pen or using surgical instrumentation remotely.
Why is this important to factor into product development?
An example best illustrates the importance of human factors engineering. Let’s say we’re going to build something that provides a means to watering your plants. There are three capability requirements: to hand hold the product; to contain water; and to pour water on the plants. Three very general requirements. However, what could happen without consideration for the ability to grip is that the handle might be too bulky for the user to spill water onto the plants, or the spout could be placed facing the wrong direction preventing understanding of how to use the product. Behaviorally, if a person can’t figure out how to use the product, it won’t be used correctly. That’s a simplified way of describing something that is a very generic application.
With medical devices, what could happen is an instrument is produced such as a surgical instrument that a male surgeon can use very well because the physiology of the male hands was taken into consideration—the width of the fingers, the span of the hands etc. Put that same instrument into a female hand and there could be an issue with the female surgeon dropping the instrument or she does not have control over the instrument because of how wide or narrow the instrument may have to be expanded or contracted for it to be suitable for female usage.
In this example of using human factors, is the goal to develop a device that can be used by both males and females?
Yes, exactly. In some cases, you could develop one instrument that would be used by either a male or female. In some cases, though, it may be necessary to develop a specific instrument for each. It depends upon what the instrument is going to be used for, what the risk is for using the instrument correctly or incorrectly in terms of its intended use and environment. There are standards—ergonomics standards that are put out by the US government called the Mill Standards. Also, ANSI/AAMI put out standards called HE75:2009 that looks at ergonomic and, also the cognitive and behavioral aspects.
Where in the product development cycle do you get involved?
It’s considered most effective at ideation through concept development and post market vigilance. We work with companies that have an idea of what they want to do and who their users are. We help them refine the idea and the user set that will be potentially using their product. That means looking at what they are doing now, what have they been using and where. Current problems are identified
Can you share examples of interesting devices that had unexpected findings to give us a greater understanding of how human factors impacts development?
Yes. I’ll start with a single-use, pre-filled syringe for medication injection. The company asked for an evaluation because FDA said the company had done preference research but not performance or behavioral research. The device had a couple of nuances. When the patient removed the tab and pressed it up against their leg to inject the medication, the device had to remain in place until hearing a click and feeling a stinging sensation—an indicator that the needle had penetrated the skin and was injecting the medication. After holding it for ten seconds to inject the medication, it would be removed and recapped. The device was designed so that once it was removed, the needle would retract. Sounds simple, right? Instead, there were some problems.
The cap had two little indentations where it met the body of the injector. The way it was built, the cap was very difficult to pull off. Since the medication injected by this device was for people with dexterity problems, that was an issue. Another I was listening for a click and feeling a sting. A person’s natural reaction when they feel a sting is to stop doing what caused it. Not to continue the procedure. In testing, many people removed the needle which prevented its retraction causing the medication to continue flowing. Attempts to recap failed because the needle was still exposed. The manufacturer had not done any previous testing and was already in production with millions of dollars of devices ready for shipment and distribution. Now that manufacturer works with HIrLan at the beginning of ideation.
There have been similar situations, but this example was the most blatant with no consideration of ergonomics to pull off cap or the necessary force to engage the needle. Cognitive issues weren’t considered either—once people feel a sting and they can stop the discomfort, that’s exactly what they will do. In this case that meant removing the needle before it was ready to retract. And, they didn’t think about behavior of the patient who knew the cap had to be put back on but could not do so. All three human factors were not adequately addressed in this example.
The fact that FDA questioned this company’s submission, is performance testing a requirement of the FDA?
Since 2010 the FDA has been extremely strict about it. It’s not just pre-built syringes. It’s according to what the classification of the device is—all class two and three, and some class one. A CE mark is also required. It’s formally required to do a summit test at the end, but it’s also inferred that companies will do a formative test—small tests throughout the development cycle because FDA is looking for the data at the time of submission.
Was there a specific event in 2010 that prompted the strict submission requirements?
Yes, a particular infusion pump that had not been evaluated for human factors caused deaths in some cases.
Can you explain how your background has helped you in your work with human factors engineering?
The traditional training is in experimental or research psychology with internships in a variety of different verticals. Some people stay in one vertical while others expand to other areas. My preference was to explore a variety of verticals because I found that experience in software verticals for example helped with medical devices that are using embedded software or software applications. Just to clarify, the research or experimental psychology Ph. D is cognitive psychology, not clinical.
Are there any trends happening now in human factor engineering?
Yes, there are a few. The first is a shortage of qualified people. As a result, caution needs to be exercised in selecting a human factors company to avoid questions from FDA or EU to show resumes or vitas. There is also a trend of people trying to get into the field who are taking shortcuts. Be careful to select a qualified company for testing and review of device design. Another trend is that in addition to it being a requirement, companies are realizing the value of human factors engineering: that it shortens the development cycle if the use of it is included from the beginning. Some companies have an internal HF department that manages external people for testing and there are others that have internal testing and regulatory affairs people. There are others that outsource everything—both startups and major companies.
What is the key takeaway that you would offer to a medical device company?
To clearly define: users, the intended use, and what the intended environment is. It’s important to establish these criteria at the very beginning and document any changes. Including human factors at the onset of ideation will produce a timelier and more efficient product with greater potential for approval. Also, the FDA is requesting more and more that clinical testing for both medical devices and pharma be done prior to phase three, because how that drug is administered could mean the difference whether it is effective or not.